Korean Shipbuilding: a fascinating story of middle power influence
Free issue. The heady atmosphere at the recent signing ceremony for the delivery of the Shinchaeho-class attack submarine, built by Hyundai Heavy and observed by officials from 9 countries, symbolized both the triumphs and tribulations facing Korea's strategically critical shipbuilding industry.
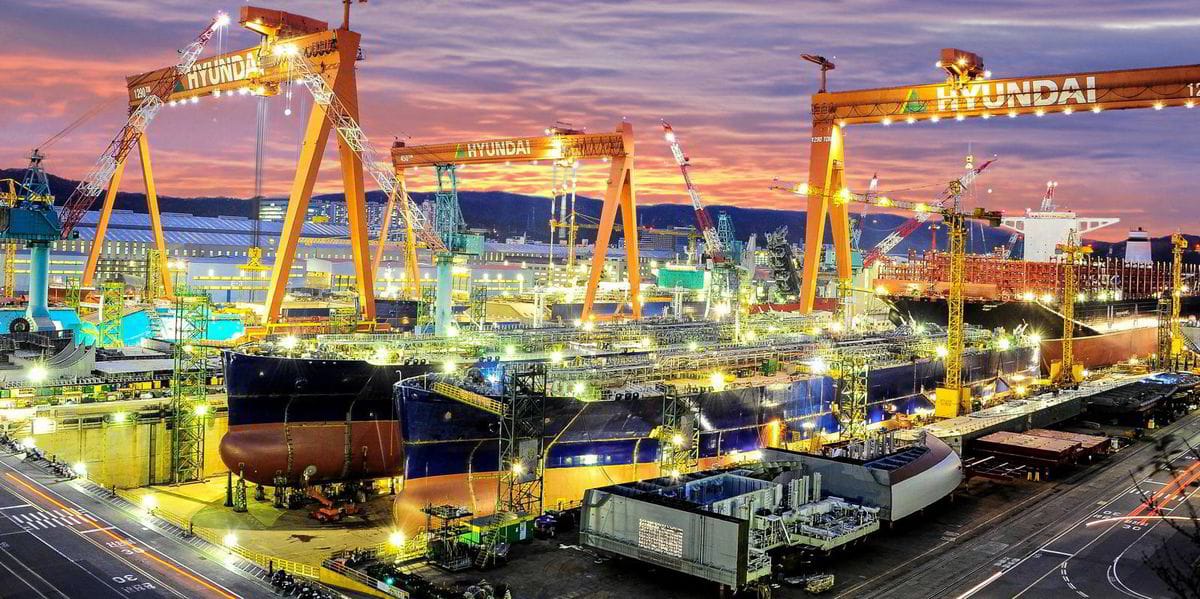
Focus on Korea series on South Korean Industries
Readers, this article is the first of a series that will examine the most important industries in South Korea. Our regular updates are ongoing, with certain issues continuing the series.
This is a free article - now and then Focus on Korea makes an article free for all readers. Enjoy.
The heady atmosphere at the recent signing ceremony for the delivery of the Shinchaeho-class attack submarine, built by Hyundai Heavy and observed by officials from 9 countries, symbolized both the triumphs and tribulations facing Korea's strategically critical shipbuilding industry. On one hand, the 3000-ton sub, designed and built almost entirely with homegrown technology as part of Korea's 3 trillion won first indigenous submarine project, showcases the incredible progress the nation has made from a virtual non-entity in shipbuilding just 50 years ago to the undisputed leader in high-tech, high-value vessels.
On the other hand, the need to proactively court foreign navies for submarine exports underscores the challenges Korea faces in sustaining its hard-won leadership in an industry characterized by long, deep cyclical swings, intense competition, and geopolitical risk. While Korean shipyards bask in a 2-3 year order backlog that has them on track to post record profits, there is a keen awareness that in shipbuilding, booms often sow the seeds of future busts.
"We are in an unprecedented supercycle thanks to the rapid rebound in global trade after the pandemic and the massive pent-up replacement demand for new ships, especially LNG and container carriers," said Lee Jae-sun, an analyst at Mirae Asset Securities in Seoul. "Korean shipyards are uniquely positioned to capture the lion's share of these high-value orders thanks to their technological dominance, economies of scale, and strong customer relationships."
Indeed, for an industry that was on life support just 5 years ago, the facts on the ground are astounding. In 2023, Korean builders won $75 billion in new orders, up 25% from 2022 and over 10 times the 2019 level. New orders for LNG carriers, a highly complex ship type where Korea enjoys over 80% global market share, nearly tripled to $30 billion as energy majors like QatarEnergy and Shell placed mega-orders to support their LNG expansion projects. Soaring container freight rates also unleashed a spree of orders for supersized 24,000 TEU boxships, with virtually all of the contracts going to Korean yards.
The blockbuster year cemented Korea's restored status as world's top shipbuilding nation, claiming 45% of global orders compared to 37% for China. More importantly, Korea now commands an estimated 70-80% share of the market for high-margin, technology-intensive vessels such as LNG and LPG carriers, supersized containerships, Arctic-class tankers, and floating production systems, while ceding the low-end bulker and general cargo ship segments to cost-focused Chinese yards.
"The key to Korea's competitiveness is the unsurpassed ability of our shipbuilders to deliver highly complex vessels that require top-notch engineering, project management, and quality control," said Park Joon-soo, secretary general of the Korea Offshore and Shipbuilding Association (KOSHIPA).
The fruits of this were exemplified in 2023 by milestones like Daewoo Shipbuilding (now Hanwha Ocean) delivering the first ever Korean-built large-scale submarine to Indonesia, Samsung Heavy completing the world's largest containership at 24,500 TEU for Evergreen Marine, and Korea Shipbuilding and Offshore Engineering beginning construction of the first icebreaking LNG carrier to be powered solely by LNG. These demonstrated not only Korea's technological supremacy but also the benefits of its strategy to dominate the high-end, future-facing segments of the shipbuilding market.
Perhaps nowhere is this more evident than in the naval segment. The Korean government's $35 billion naval buildup plan, centered on the development of light aircraft carriers and Aegis destroyers, has been a massive boon for Korean naval shipbuilders. Hyundai Heavy is building the first two KDX-III Batch II destroyers featuring the Aegis system, while Daewoo/Hanwha is taking the lead on the LPX-II light carrier project. The submarine force is also expanding with the new Jangbogo-III 3000 ton attack subs and a next-gen 4000 ton class in the works.
The benefits go beyond the domestic market. The Jangbogo-III subs are already generating serious export interest from countries like Indonesia and the Philippines, while the Daegu-class frigates have been sold to Thailand. By building a top-to-bottom naval shipbuilding capability spanning submarines to carriers, Korea is positioning itself as a credible alternative to traditional naval exporters like France, Germany and Spain, especially for Southeast Asian and Middle Eastern buyers.
"Countries want a full package of naval capabilities but from a partner they can trust, and our shipbuilders can deliver that," said RoK Navy Captain Kim Tae-hyun. "We're on track to grow KRW 8 trillion in naval exports over the next decade."
This lucrative defense segment provides some welcome diversification for Korea's shipbuilders, but the bulk of their order books are still in commercial ships. And here they are making equally bold bets on revolutionary new technologies to comply with increasingly stringent carbon emissions rules from the UN International Maritime Organization (IMO).
Korean yards are pioneering the development of dual-fuel engines that can run on both LNG and zero-carbon fuels like ammonia and hydrogen. Samsung Heavy has already delivered the world's first LNG-fueled VLCCs to European owners, while Korea Shipbuilding is building ammonia-ready LPG carriers. Hyundai Heavy, meanwhile, is partnering with local green energy firms to establish a dedicated supply chain for marine biofuels.
"The IMO emissions rules are the biggest force reshaping shipping, and Korean shipbuilders are determined to seize first-mover advantage," said Lee Sung-bo, an analyst at Hanwha Investment and Securities. "Yes, the technologies are unproven and the costs high, but the payoff in terms of dominating the inevitable replacement cycle for greener ships will be immense."
Government support has been crucial in empowering Korea's shipbuilders to take these risks. Seoul designated shipbuilding as a strategic national industry and has showered it with every form of aid, from R&D funding to financing to diplomatic lobbying abroad. The recent $2.25 billion government-backed order by QatarEnergy for LNG ships from Samsung, Hanwha Ocean, and Korea Shipbuilding & Offshore Engineering (KSOE), for example, was the direct result of President Yoon's sales diplomacy with the Emir of Qatar.
But ultimately, it is on the "hard power" side that the government's impact is most keenly felt. Roughly one-fifth of Korean shipbuilders' revenue now comes from military projects, and this could exceed one-third by 2030. The submarine, destroyer and frigate orders for the RoK Navy are the bedrock that enables the investments in facilities and engineering needed to keep Korea ahead in the commercial arena as well.
Indeed, it is this intimate linkage of commercial and military shipbuilding capabilities, in coordination with proactive policy support and a relentless drive to pioneer new marine technologies, that makes the Korean model so formidable. No other shipbuilding nation boasts this triple threat.
Yet for all their success, Korea's shipbuilders have no time to rest on their laurels. The industry's Achilles heel has always been its vulnerability to global trade downswings, which given slowing economic growth in the US, Europe and China, may be looming just over the horizon. Already there are signs of a slowdown in new orders in 2024 as skittish owners take a wait-and-see approach.
Longer-term structural risks also cloud the picture. Potential shifts in global supply chains and the rise of reshoring could dampen trade growth and ship demand. Geopolitical tensions with China over everything from THAAD to Taiwanese independence could disrupt market access and technology partnerships. And the cost and technical challenges of developing zero-carbon vessels could delay fleet replacement plans.
Most seriously, the current order boom is spurring another round of capacity expansion, especially at Chinese yards eager to unseat the Koreans. The addition of millions of tons of new docks and berths may be setting the stage for a repeat of the severe overcapacity that plagued the industry in the mid-2010s, leading to a wave of layoffs and multi-billion dollar bailouts.
To hedge against this, Korea's Big 3 shipbuilders are exploring some radical business model shifts. The planned mega-merger of KSOE and Hanwha Ocean would create a shipbuilding behemoth with unrivaled scale and pricing power. Hyundai Heavy is moving into shipping and finance to lock in long-term captive customers and revenue streams. And all are aggressively expanding into offshore wind installation, marine battery systems, and other new growth segments to diversify away from conventional shipbuilding.
The companies are also going all-in on digitalization and automation under the "Industry 4.0" paradigm to boost productivity and cut costs. From AI-powered design tools to 3D printing to human-robot collaboration on the docks, Korean shipyards are determined to extend their technology edge.
How this digital transformation unfolds may ultimately determine whether a rising tide continues to lift all Korean shipbuilders, or whether a widening gulf emerges between forward-looking leaders and those stuck in analog mode. What is certain is that Korean shipbuilding is at an inflection point, facing a disruptive decade that will put its newfound dominance to the test.
"This is the most pivotal moment for Korea's shipbuilders since they overtook the Europeans and Japanese back in the 1990s and 2000s," said the grizzled Lee Jong-soo, former chairman of Hyundai Heavy Industries and an icon of the industry. "The decisions we make now on technology, business models, and political partnerships will chart our course for the next 25 years. One thing I know from having seen many cycles - now is not the time for complacency, but for bold action to secure our leadership."
One area where bold action is clearly being applied is in the defense realm. Flush with cash from commercial orders, Korea's Big 3 are doubling down on the research and capex needed to expand their naval product lineup and challenge the Europeans. The successful exportation of the Jangbogo-III submarine would be a major coup and beachhead for greater market access in Southeast Asia.
At the same time, policymakers are working to more fully integrate naval and commercial shipbuilding to better coordinate fleet plans, technology roadmaps, and worker training. The recently established Korean Naval and Commercial Shipbuilding Promotion Agency, modeled on a smaller scale after the US's MARAD, is tasked with implementing this vision of Korea as an integrated civilian and military maritime power.
"Just as the US and China consider naval shipbuilding a key national security capability, so too are we moving in that direction to further strengthen the competitiveness of our marine industries," said Moon Sung-hyun, the former Chief of Naval Operations who heads the new agency. "By 2035, we aim to grow our indigenous content in naval ships to over 90% and establish Korea as a top 5 naval exporter globally."
This rising emphasis on naval shipbuilding as a pillar of Korea's maritime power and geoeconomic position is matched by an equally proactive approach to climate change. The "2050 Green Ship-K" initiative, a joint project of government and industry, has set hugely ambitious targets of reducing carbon emissions from Korean-built ships by 50% in 2030 and 70% in 2050.
Meeting those goals will require a massive replacement cycle for the current 90,000-ship global fleet, with a focus on emissions-free propulsion systems. Korean shipbuilders are determined to spearhead the charge.
"Decarbonization is a direct threat to our Chinese competitors given their reliance on low-cost, conventional designs," said KOSHIPA's Park. "But for us, it's a golden opportunity to make our technological superiority count and cement our position as the dominant force in the new green shipping paradigm."
The world will be watching to see if Korea's shipbuilders can deliver on that audacious promise. What is certain is that the economic and security outcomes for Korea could not be greater. In an ocean of both risk and possibility, they must now prove their skill at navigating the most momentous crosscurrents to confront their industry in half a century.